1、浸膏粘性过大,制粒成型困难
中药颗粒剂生产制备过程中,浸膏本身往往起到粘合剂的作用,当浸膏粘性过大,浸膏量吸附辅料相互聚集成细小团块,若浸膏量小不易搅拌均匀。若浸膏量大则物料易聚结成较大的团块,使制粒发生较困难,制粒时筛网上会出现“疙瘩”。并且制得颗粒容易产生花斑,以上现象可以选用以下途径来解决:
①从浸膏的提取工艺着手,根本上改善浸膏粘性。在保证药效及有效成分定性、定量质量检测的前提下,采用正交设计试验,优选提取与精制工艺,在zui大限度保留有效成分的同时更多地去除无效成分(里含较多的粘性物质),如采用包煎或水提醇沉、过滤等方法使粘液质、蛋白质、多糖等粘性成分不提出或除去。
②在剂量处方允许的范围内,选用适宜的辅料,并确定辅料的种类、用量及加入方法。
③可以将浸膏的相对密度增大,降低其含水量使之成为稠浸膏或者直接采用真空干燥或喷雾干燥使之呈干浸膏后粉碎,再与辅料混匀加入高浓度的乙醇迅速制粒,此时软材易于挤压过筛,也易干燥。采用这两种方法都要对乙醇浓度和用量进行优选。
④浸膏粘性大而用量小时,在加入润湿剂之前,浸膏应与辅料充分搅拌均匀,从而防止搅拌不均匀而产生相互聚集呈细小团块进而产生颗粒花斑,为了达到其充分搅拌均匀的目的,我们可采用浸膏用适宜润湿剂稀释后分次缓慢加入或将稀释后的浸膏呈雾状喷入,制成软材。
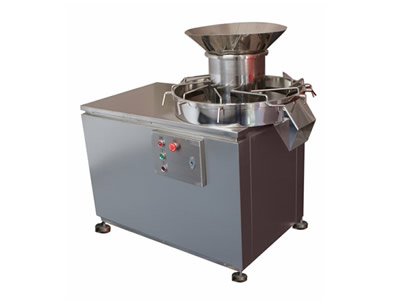
⑤浸膏粘性大且用量大时,我们可以采用二次制粒法,即先取半量以上(约2/3左右)的浸膏与全量的辅料混合制粒,此次操作可以不考虑颗粒的一次得率,烘干后,粉碎成粉状再与余下的浸膏混合制粒。
⑥改变制颗粒方法,如采用一步制粒法或浸膏稀释后用喷雾制粒法制粒。
2、湿法制粒所制的颗粒过粗、过细、头粉多、颗粒一次得率低
这种现象产生原因及解决办法主要有以下几点:
①软材未搅拌均匀。解决方法可采用:a.延长搅拌时间;b.改变物料加入方式;c.改变辅料处方的组成。
②润湿剂乙醇含量偏高,为了降低浸膏或干膏粉粘性,为了便于物料制粒常采用高浓度乙醇作润湿剂,造成开始制得的颗粒易散,细粉量多,而后逐渐的由于部分乙醇挥散,软材粘性增加,制粒困难并且湿粒常成条状,颗粒头子多,zui终导致颗粒颗粒过粗、过细,头粉量多,一次得率低。解决办法有:a.降低乙醇浓度,适当增加辅料用量,密闭操作,快速制粒,b.控制软材搅拌时间,(以软材颜色刚好加深,握之成团,捏之即散,色泽均匀为经验掌握),立即快速制粒,刚开始制粒时,制粒有筛网可适当放松,加料速度为快速,若湿粒仍较散,可进行二次过筛制粒。随后,控制筛网的松紧度和软材加料速度,使湿颗粒完整。当制出的湿颗粒呈条状,或制粒困难时,可以更换筛网,若问题还存在,可以加入适量的95%乙醇到软材中,继续搅拌片刻,再进行制粒,此时,也可加入适量的尾料粉碎后粉和润湿剂,再继续搅拌制呈软材。用此法,可以解决因润湿剂乙醇挥散造成的问题,制得的颗粒粒径大小均匀,不过实际生产操作中,还应根据物料性质以及环境等因素的不同,来改变乙醇的浓度和用量。
③筛网的选择不当。解决方法:根据物料的性质选择筛网的规格和筛丝的直径和材质。如物料松散,粘性小,可采用筛丝直径大(0.4-0.6mm),材质也可偏软如镀锌铁丝、尼龙丝等,筛网的孔径可以偏小,(颗粒剂一般12-14目)如果物料的粘性大,则选用筛网直径相对小(一般0.2-0.4mm)材质要坚硬(如镀锌钢、不锈钢等)筛网的孔径可以偏大(颗粒剂一般10-12目)
④其他原因:如操作环境湿度较大,因此导致边制粒边吸湿,其解决办法为:改善环境,加快制粒速度。
沸腾干燥时,风量未调节好或者进料速度太快导致颗粒粘结底板,在干燥床内不呈沸腾状,而导致头子太多,解决办法:控制进料速度和进料量以及调节好用量,常抖动布袋,翻动底板颗粒,使其在沸腾床内保持沸腾状态。